Extrude Hone’s advanced surface solutions help to eliminate defects from the surfaces of additively manufactured components and therefore contribute to improved component fatigue properties.
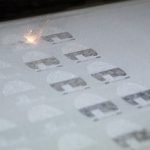
Partially Sintered Material
The inherent process of melting and bonding powder can result in rough surface condition on the outer skin of a build. This is a result of partially bonded powder on the surface. This can affect product quality and needs to be removed so that particles do not detach during the lifecycle of the product. Loose metallic particles can be particularly harmful in the case of hydraulic components and medical implants. Extrude Hone has multiple processes that are well documented as being some of the most efficient methods of removing the partially sintered material both internally and externally.
Improved Surfaces for More Efficient Flow
Compared to subtractive manufacturing methods such as CNC milling, additive manufacturing technologies produce components with relatively rough surfaces. In applications where a liquid or gas flows over the surfaces of the component, roughness can create turbulent flow which affects the efficiency of components or even whole systems. Extrude Hone’s processes reduce surface roughness in additively manufactured gas turbine components, fuel system components and hydraulic components, allowing for more laminar flow and therefore improved efficiency.
Extrude Hone’s processes reduce surface roughness in additively manufactured gas turbine components, fuel system components and hydraulic components, allowing for more laminar flow and therefore improved efficiency.
Improved Surfaces for Fatigue Strength
Parts produced by 3D printing technologies can contain defects which propagate cracking and can lead to complete component failure. Extrude Hone’s advanced surface solutions help to eliminate defects from the surfaces of additively manufactured components and therefore contribute to improved component fatigue properties. In highly-stressed applications such as structural components and engine components for aerospace and orthopedic components for medical, this can make the difference between a part that works and a part that fails with catastrophic consequences.
Support Structures Removal
In metal 3D Printing, Support Structures are key in obtaining a stress-free, accurate, complex part. These often must be placed in hard-to-reach areas, constraining removal by machining, therefore increasing cost and complexity to produce the final component. Manual support removal is not fully repeatable, can be extremely time-consuming and poses health and safety concerns. By combining Advanced TEM Processes with specially-engineered support structures, we can completely remove support material in most channel-like features. This is achieved in a matter of seconds and can be performed on multiple channels simultaneously, reaching areas inaccessible by other means.
Master of Building and Finishing Strategy
There are many hidden elements such as machine usage, consumables and labor time that have a significant impact on the cost of producing an AM part. One consideration is build speed; a faster build will result in a lower cost and also a higher productivity. All being equal, a higher build speed results in a rougher surface and higher finishing costs. Finding the right balance between build time and finishing time is key to maximize productivity. Combining our finishing technologies with our AM capacity, we deliver one-stop-shop excellence to our customers, finding the winning finishing strategy that will push quality and productivity to the next level.